Nature is known for developing lightweight yet tough materials using limited, modest materials arranged into ingenious architecture. Take nacre, for example. More commonly known as mother of pearl, the shiny inner lining of some mollusks’ shells is an organic-inorganic composite comprised of a 3D brick-and-mortar pattern made of sheets of hexagonal tablets of aragonite, a hard mineral, glued together by a soft, hyper-elastic biopolymer.
Although aragonite tablets are highly brittle, the biopolymer’s flexibility allows them to slide in response to tensile stress, making nacre a tough material that can deform significantly before fracturing. Now, researchers from Princeton University’s Department of Civil and Environmental Engineering have created a new, superior cement composite by mimicking the architecture of natural nacre.
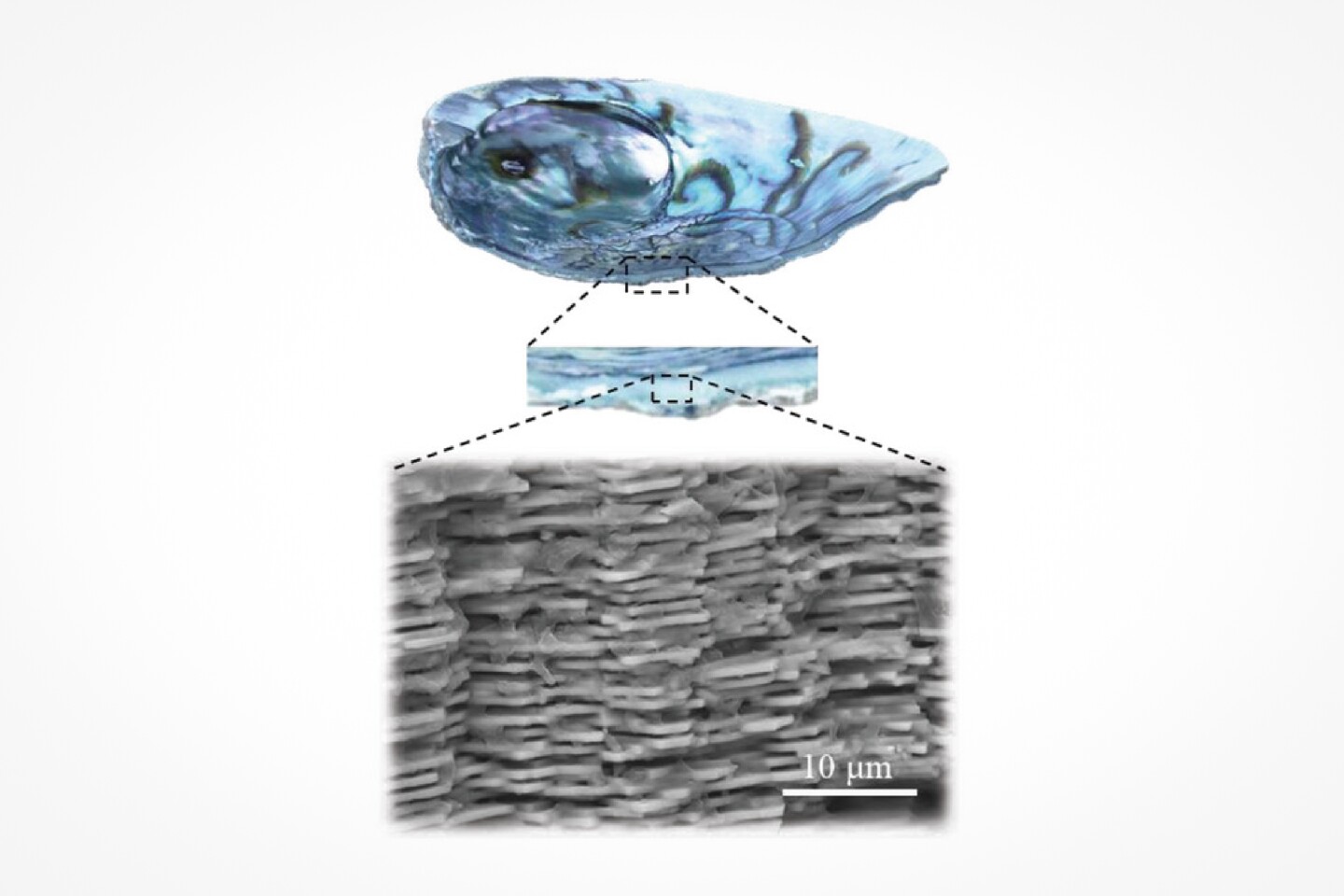
Gupta et al.
“This synergy between the hard and soft components is crucial to nacre’s remarkable mechanical properties,” said Shashank Gupta, a Princeton Engineering graduate student and the study’s lead author. “If we can engineer concrete to resist crack propagation, we can make it tougher, safer and more durable.”
To make their nacre-like composite material, the researchers created hexagonal tablets from cement paste sheets and layered them, separated by polyvinyl siloxane (PVS), which acted as the hyper-elastic biopolymer. The composite’s mechanical response was then tested using beams made from the material and compared to beams made with solid (monolithic) cast cement paste.
The beams were subjected to a notched three-point bending (3PB) test, where downward pressure is placed in the middle of the beam and upward pressure at each end, to evaluate crack resistance or fracture toughness. The tests showed that the cast cement paste ‘hard’ beams were brittle; they broke suddenly and completely when they reached failure point because they had no flexibility (ductility). In contrast, the nacre-like composite beams demonstrated 19 times the ductility and 17.1 times the fracture toughness of the control beams, while retaining nearly the same strength.
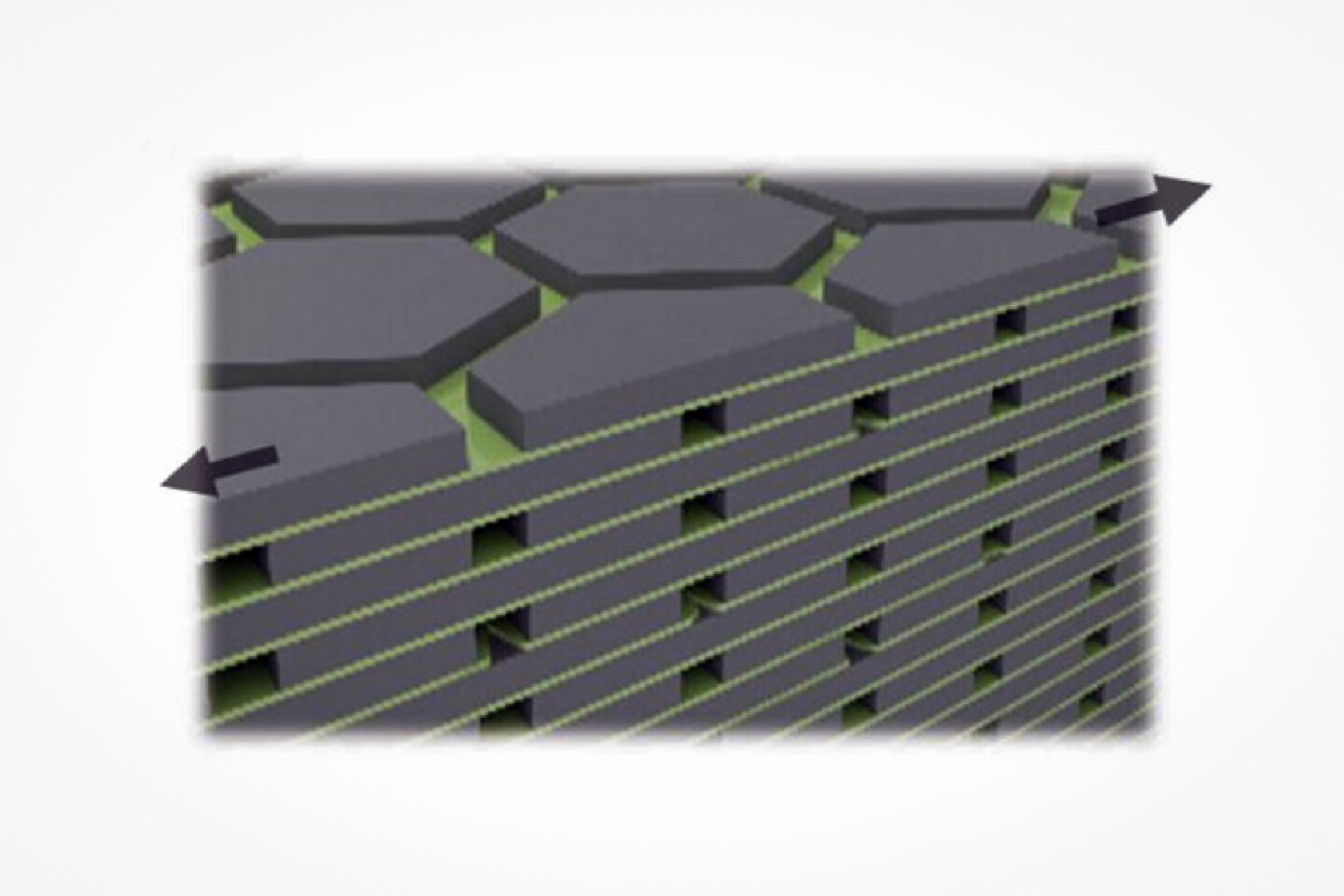
Gupta et al.
“Our bio-inspired approach is not to simply mimic nature’s microstructure but to learn from the underlying principles and use that to inform the engineering of human-made materials,” said Reza Moini, head of the Architected Materials and Additive Manufacturing (AM2) lab at Princeton and the study’s corresponding author. “One of the key mechanisms that makes a nacreous shell tough is the sliding of the tablet at the nanometer level. Here, we focus on the mechanism of tablet sliding by engineering the built-in tabulated structure of cement paste in balance with the properties of the polymer and the interface between them. In other words, we intentionally engineer defects in the brittle materials as a way to make them stronger by design.”
Of course, these results were produced in the lab. The researchers plan on testing the bioinspired cement composite in real-world settings and are investigating whether its mechanical properties can be used to increase the crack resistance of other materials, such as concrete and porcelain.
“We are only scratching the surface,” Moini said.
The study was published in the journal Advanced Functional Materials.
Source: Princeton Engineering